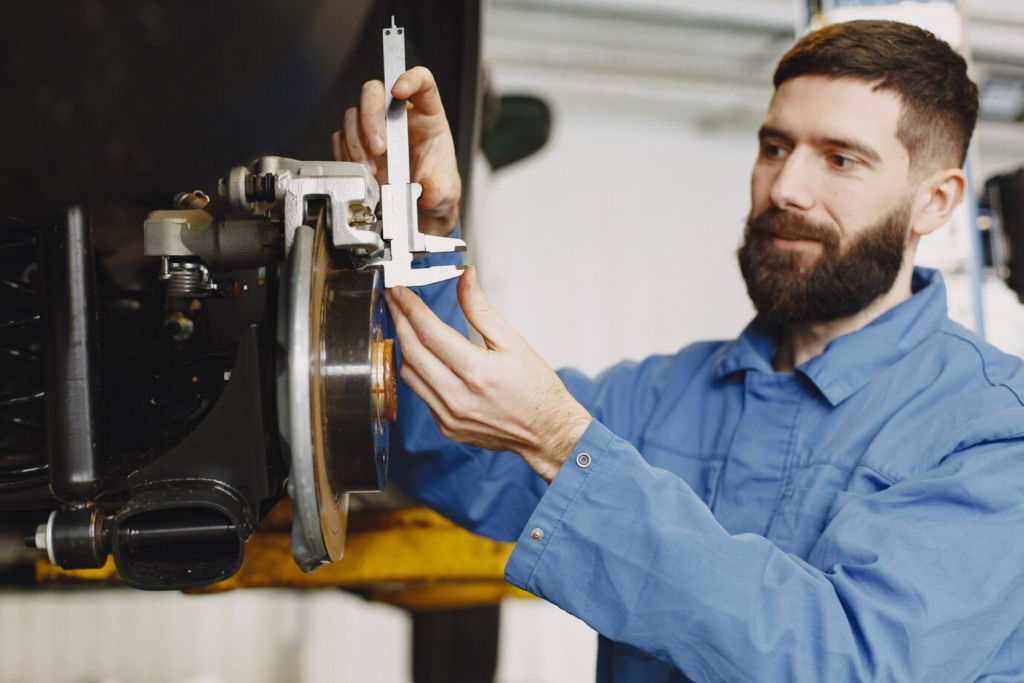
The longevity and efficiency of rotating machinery are more important than ever in the fast-paced industrial environment of today. In many industries, including manufacturing, energy, aviation, and transportation, rotating machinery—from fans and turbines to motors, pumps, and compressors—is essential. However, because of their dynamic nature, these components are susceptible to imbalance, a prevalent but frequently disregarded problem that can result in significant wear, inefficiencies, and catastrophic failures. Expert dynamic balancing is useful in this situation. Dynamic balancing is a specialized maintenance procedure that is necessary to guarantee the safe, effective, and seamless operation of rotating components. Without it, even the most sophisticated equipment can be easily compromised, increasing downtime and necessitating expensive repairs.
Comprehending Dynamic Equilibrium
The process of modifying a rotating object’s mass distribution to allow it to spin smoothly around its axis without experiencing excessive vibration or stress is known as dynamic balancing. Dynamic balancing is perfect for complex machinery because it addresses imbalances across multiple planes, unlike static balancing, which only takes into account one plane of motion. Wear and tear, poor assembly, and manufacturing flaws can all lead to imbalances. Increased vibration, noise, and wear can result from the system becoming unbalanced due to even minor misalignment or an uneven weight distribution. To restore optimal performance, expert dynamic balancing makes sure that all possible sources of imbalance are found and fixed.
Advantages of Skilled Management
There is no one-size-fits-all method for dynamic balancing; precise execution calls for specific tools, education, and experience. To identify and fix imbalances, skilled technicians employ advanced equipment like high-precision balancing machines, laser alignment systems, and vibration analyzers. These professionals can also decipher data to find underlying issues like bent shafts, misalignment, or incorrect assembly methods. Businesses gain insights into the general health of their machinery in addition to smooth operation when they entrust dynamic balancing to experts. By taking a proactive stance, possible problems can be identified before they become serious ones, which lowers unscheduled downtime and increases equipment lifespan.
The Repercussions of Unbalance
In rotating machinery, improper dynamic balancing can have detrimental effects. Unbalanced vibrations put undue strain on shafts, bearings, and other supporting components. This may eventually lead to wear and tear on the components, early failure, and total system failures. Even small imbalances can be amplified in high-speed machinery, posing serious safety risks. Additionally, because more power is needed to keep things running, an imbalance lowers energy efficiency and raises operating costs. In industries like manufacturing or power generation, where dependability and uptime are critical, an unplanned failure brought on by imbalance can cause significant operational disruptions and financial losses. Finding expert balancing services is an investment that keeps these problems at bay and guarantees continuous operation, so make sure you check this idea out ASAP.
Uses in Various Industries
Expert dynamic balancing is required in many different industries. The accuracy of an aircraft’s rotating parts is crucial to its safety in the aerospace industry. Devastating outcomes can arise from even a slight imbalance in an engine rotor or turbine. For smooth driving experiences and long vehicle lifespans, dynamic balancing is essential for engines, wheels, and drive shafts in the automotive sector. Fans, blowers, and pumps in industrial manufacturing facilities use dynamic balancing to save energy and prevent production delays. It is essential to preserve the effectiveness of turbines and generators in power plants. Expert balancing guarantees optimal operation, safety, and sustainability regardless of the industry.
Predictive Maintenance’s Function
Dynamic balancing is ideally suited to the predictive models that are replacing reactive models in modern maintenance strategies. Predictive maintenance anticipates and stops equipment failures before they occur by using routine monitoring and data analysis. By using vibration analysis and other diagnostic techniques to identify early indicators of wear, imbalance, or structural weakness, expert dynamic balancing helps achieve this. Instead of waiting for a breakdown to happen, this enables maintenance teams to deal with problems early on. This enhances asset reliability and overall operational efficiency in addition to lowering maintenance costs. Businesses that use expert dynamic balancing in conjunction with predictive maintenance are more adaptable, competitive, and ready for any obstacles down the road.
The performance, dependability, and safety of rotating machinery are protected by expert dynamic balancing, which is much more than just a standard maintenance procedure. It is impossible to overestimate the significance of maintaining balanced equipment as industries continue to demand faster speeds, more accuracy, and higher productivity.
also read: Taste Before You Tour: The Cities Where Food Tells the Whole Story