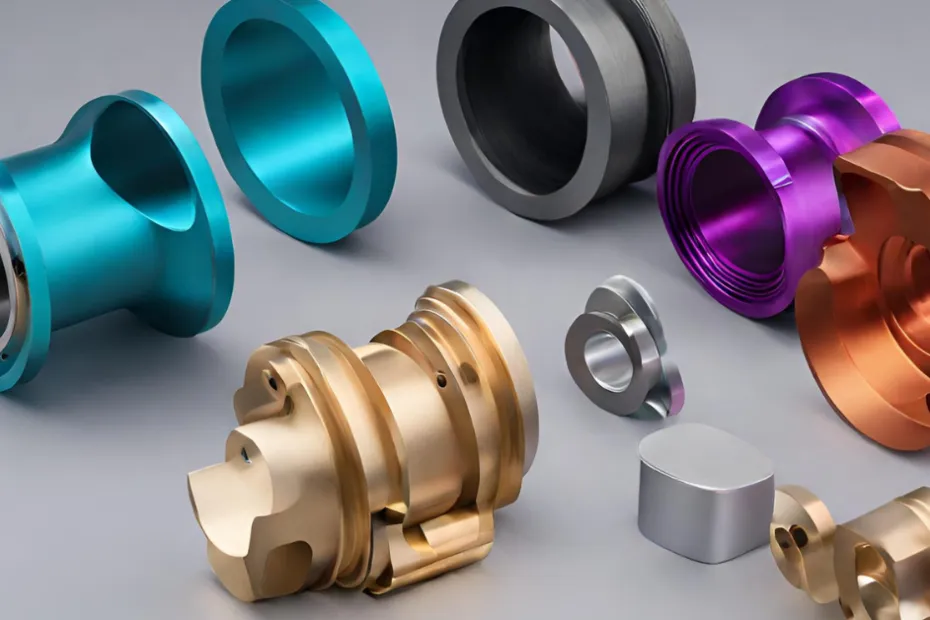
Anodized aluminum is often praised for its impressive durability and corrosion resistance, making it a popular choice in various industries. From architectural structures to consumer electronics, anodized aluminum is a material that performs well in both aesthetics and longevity. But how durable is anodized aluminum, really? Many factors contribute to its durability, and understanding the anodizing process, its benefits, and the best practices for maintaining anodized surfaces is crucial for maximizing its lifespan.
In this article, we’ll explore how anodizing works, how durable anodized aluminum truly is, and what you can do to keep it durable over time. We will also address common concerns about the longevity of anodized finishes and provide tips for maintaining their performance. Whether you’re using anodized aluminum for industrial purposes or decorative applications, this guide will provide a comprehensive look at the durability of anodized aluminum.
What is Anodizing and How It Works?
Anodizing is an electrochemical process that enhances the natural oxide layer on the surface of aluminum. This process involves immersing aluminum into an acid electrolyte bath and passing an electric current through the solution. The result is a thicker, more durable oxide layer that is integral to the aluminum, making it highly resistant to corrosion, wear, and even UV damage. Unlike paint or coatings, the anodized layer does not peel or chip because it becomes part of the aluminum itself.
The anodizing process can produce various finishes, including clear, matte, and durable anodized aluminum with colored surfaces. The ability to create a range of colors adds aesthetic appeal, while the durable layer offers significant protection. The thickness of the anodized layer can also be controlled during the process, allowing manufacturers to tailor the aluminum’s durability to specific applications. For example, thicker anodized layers are typically used for outdoor architectural components, while thinner layers may be sufficient for indoor products like consumer electronics.
Anodizing works by essentially turning aluminum into a more resilient material. The protective oxide layer that forms on the surface is highly resistant to corrosion and oxidation, unlike untreated aluminum, which can quickly develop a dull, tarnished appearance. This protective barrier is also hard and abrasion-resistant, making it an ideal solution for parts that are subject to heavy wear.
Despite its many benefits, anodizing is not without its limitations. The durability of anodized aluminum depends on various factors, including the quality of the aluminum, the anodizing process itself, and the environment in which it is used. These considerations can affect how well the anodized layer holds up over time, which leads us to the question: just how durable is anodized aluminum?
How Durable Is Anodized Aluminum?
The durability of anodized aluminum is one of its standout features, but it is important to understand what factors contribute to its long-lasting performance. The anodized layer acts as a shield against corrosion, abrasion, and even UV damage. One of the primary reasons anodized aluminum is so durable is the strength of the oxide layer, which is much harder than the base aluminum itself. This makes it an ideal choice for high-stress environments where materials are exposed to harsh conditions.
Anodized aluminum is frequently used in outdoor settings because it can withstand exposure to the elements much better than untreated aluminum. For example, architectural facades, window frames, and exterior lighting fixtures made from anodized aluminum can maintain their appearance and structural integrity for decades without significant maintenance. Even in areas with high humidity, saltwater exposure, or pollution, anodized aluminum resists corrosion far better than other materials.
That being said, the durability of anodized aluminum also depends on the thickness of the anodized layer. Thicker layers provide greater resistance to wear and corrosion, which is why industries requiring heavy-duty applications, such as aerospace and marine sectors, often use aluminum with thicker anodized coatings. On the other hand, thinner anodized layers may still offer excellent protection for indoor use or products that don’t face extreme environmental conditions.
However, it’s essential to note that while anodized aluminum is highly resistant to corrosion, it is not entirely impervious to damage. Scratches or deep abrasions can penetrate the anodized layer and expose the underlying aluminum, making it vulnerable to corrosion. Once the anodized surface is compromised, the damage cannot be easily repaired without re-anodizing the entire part.
When it comes to UV resistance, anodized aluminum performs exceptionally well. Unlike painted surfaces that can fade or peel under prolonged exposure to sunlight, anodized aluminum maintains its color and finish for years. This is why anodized finishes are often chosen for outdoor applications like signage, building exteriors, and automotive parts.
A good example of how anodized aluminum’s durability is valued can be seen in its use by companies like Zintilon manufacturer, which provides high-quality anodized aluminum products for demanding applications. By focusing on precision and process control, manufacturers like Zintilon can ensure the durability of their anodized products meets the highest industry standards.
How to Keep Anodized Aluminium Durable
Even though anodized aluminum is highly durable, proper care and maintenance can extend its lifespan significantly. Keeping anodized aluminum in top condition is relatively easy, but it does require some attention to detail, particularly in harsh environments.
One of the most effective ways to keep anodized aluminum durable is through regular cleaning. Over time, dirt, grime, and pollutants can accumulate on the surface, which can compromise the anodized layer’s protective qualities. Cleaning anodized aluminum with mild soap and water can help remove these contaminants without damaging the surface. It’s important to avoid using abrasive cleaners or scrubbers, as they can scratch the anodized finish. For tougher stains, a non-abrasive cleaner designed for aluminum can be used.
Another crucial aspect of maintaining anodized aluminum is protecting it from chemical exposure. Certain chemicals, such as strong acids or alkalis, can degrade the anodized layer and reduce its durability. If anodized aluminum is used in an industrial setting where exposure to harsh chemicals is likely, applying a protective coating or regularly inspecting the aluminum for signs of damage can help prolong its life.
Additionally, keeping anodized aluminum away from harsh physical impacts can prevent scratches and dents that compromise its surface. While the anodized layer is highly resistant to wear, it is not indestructible. Areas with heavy traffic or potential for collisions should be monitored, and protective measures such as padding or barriers may be implemented to safeguard anodized surfaces.
It’s also worth considering the environment in which the anodized aluminum will be used. While it is well-suited for outdoor environments, prolonged exposure to extreme conditions such as saltwater or industrial pollutants can eventually wear down the anodized layer. In such cases, applying a sealant to the anodized surface can add an extra layer of protection, helping the aluminum withstand environmental stress over the long term.
For high-wear applications, ensuring the anodized layer is of sufficient thickness can make a significant difference. Thicker anodized coatings are more resistant to scratches and wear, making them ideal for surfaces that will experience frequent use or heavy contact. Consulting with reputable manufacturers, like Zintilon manufacturer, to obtain high-quality, durable anodized aluminum products can ensure that the anodizing process is done correctly, providing optimal protection for the material.
Finally, inspecting anodized aluminum regularly for signs of wear, corrosion, or damage can help address issues before they become significant problems. Early detection and appropriate maintenance can ensure the longevity and durability of anodized aluminum for years to come.
Conclusion
Anodized aluminum is celebrated for its durability, offering superior resistance to corrosion, wear, and UV damage compared to untreated aluminum. The anodizing process enhances the material’s natural oxide layer, providing long-lasting protection that makes it suitable for a wide range of applications, from architecture to consumer products. While the durability of anodized aluminum is impressive, it is not invincible. Factors like the thickness of the anodized layer, the environment, and proper maintenance all play a role in determining how long anodized aluminum will last.
By understanding how anodizing works and the factors that contribute to its durability, you can make informed decisions about where and how to use anodized aluminum. Regular cleaning, protecting against chemical exposure, and choosing high-quality anodized products from trusted manufacturers like Zintilon manufacturer are all steps you can take to keep anodized aluminum durable for as long as possible.
With the right care, anodized aluminum can provide decades of reliable performance, maintaining both its appearance and functionality. Whether you’re using it for industrial, architectural, or personal purposes, the durability of anodized aluminum makes it a highly valuable material in a variety of fields.