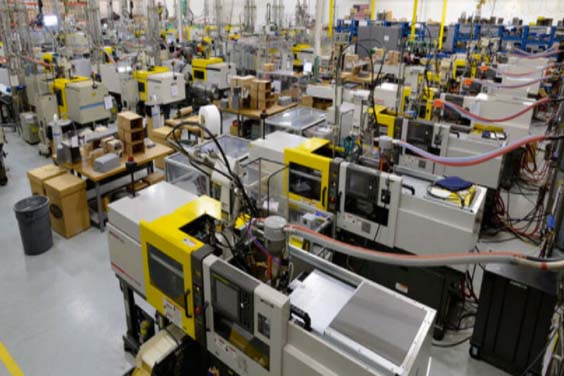
Injection molding is a pivotal manufacturing process in the production of plastic parts, components, and products. An injection molding manufacturer specializes in this method, offering services that range from the design and development of molds to the mass production of plastic items. This article delves into the world of injection molding manufacturers, exploring their role, the processes they use, and the importance of choosing the right manufacturer for specific needs.
HITOP – a leading injection molding manufacturer based in China. The website is in English, targeting global clients with services like mold design, rapid prototyping, injection molding, and more.
Understanding Injection Molding
Injection molding is a manufacturing technique that involves injecting molten plastic into a mold cavity. The process begins with the melting of plastic pellets, which are then injected into a precisely designed mold under high pressure. For example, a drink manufacturer UK might use this method to create various components. Once the plastic cools and solidifies, the mold is opened to reveal the final product. This process is repeated to produce large quantities of identical items with high precision and consistency. Injection molding is widely used across various industries, including automotive, consumer goods, electronics, medical devices, and packaging. The ability to produce complex shapes, intricate details, and a wide range of sizes makes it a popular choice for manufacturers.
Key Components of Injection Molding
Several critical components are involved in the injection molding process. The first is the mold itself, which is custom-designed to create the desired shape of the final product. Molds are typically made from high-quality steel or aluminum and can be designed to produce multiple parts in a single cycle. The injection molding machine is another essential component. This machine consists of a hopper, a heating barrel, a screw or plunger, and a mold clamping unit. The plastic pellets are fed into the hopper, where they are heated and melted before being injected into the mold. Finally, the plastic material used in injection molding plays a significant role in determining the quality and properties of the final product. Commonly used plastics include polyethylene, polypropylene, polystyrene, and acrylonitrile butadiene styrene (ABS). The choice of material depends on factors such as the product’s intended use, mechanical properties, and cost.
The Role of an Injection Molding Manufacturer
An injection molding manufacturer is responsible for managing the entire production process, from the initial design phase to the final delivery of finished products. This involves several key steps, including mold design and manufacturing, material selection, process optimization, and quality control. Mold design is a critical aspect of the injection molding process. The manufacturer works closely with the client to create a mold that meets the specifications of the final product. This involves detailed computer-aided design (CAD) work, as well as the use of sophisticated simulation software to predict how the plastic will flow within the mold. Once the mold design is finalized, the manufacturer produces the mold using precision machining techniques. This step requires high levels of accuracy, as even the smallest deviation can impact the quality of the final product. The manufacturer also selects the appropriate plastic material based on the product’s requirements. This decision is crucial, as different materials offer varying levels of strength, flexibility, and resistance to heat and chemicals. During the production phase, the manufacturer continuously monitors and optimizes the injection molding process to ensure that each part meets the desired specifications. This includes adjusting parameters such as injection speed, temperature, and pressure to achieve the best possible results. Quality control is another vital function of the injection molding manufacturer. Rigorous testing and inspection procedures are implemented to identify and address any defects or inconsistencies in the final products. This ensures that only high-quality parts are delivered to the client.
Advantages of Working with a Professional Injection Molding Manufacturer
There are several benefits to partnering with a professional injection molding manufacturer. One of the most significant advantages is the ability to produce large quantities of parts with consistent quality. Injection molding is highly efficient, allowing manufacturers to produce thousands or even millions of identical items with minimal variation. Another advantage is the cost-effectiveness of injection molding for high-volume production. Once the initial mold is created, the per-unit cost of producing plastic parts is relatively low. This makes injection molding an attractive option for companies looking to manufacture products at scale. Working with an experienced injection molding manufacturer also provides access to expertise and technical support. Manufacturers bring a wealth of knowledge to the table, helping clients navigate the complexities of the injection molding process and make informed decisions about materials, design, and production. Additionally, injection molding manufacturers often offer value-added services such as assembly, packaging, and logistics support. This allows clients to streamline their supply chain and reduce the time and effort required to bring products to market.
Choosing the Right Injection Molding Manufacturer
Selecting the right injection molding manufacturer is crucial for the success of any production project. Several factors should be considered when evaluating potential partners, including experience, capabilities, quality standards, and customer service. Experience is a key indicator of a manufacturer’s ability to deliver high-quality results. Manufacturers with a proven track record of successful projects are more likely to have the expertise and resources needed to meet complex requirements. Capabilities are another important consideration. It’s essential to ensure that the manufacturer has the equipment, technology, and capacity to handle the specific needs of the project. This includes the ability to work with the desired materials, produce parts of the required size and complexity, and meet production deadlines. Quality standards should also be a top priority. Reputable injection molding manufacturers adhere to strict quality control processes and are often certified to industry standards such as ISO 9001. This ensures that the final products meet the highest levels of quality and reliability. Finally, customer service is a critical factor in choosing an injection molding manufacturer. A reliable manufacturer should be responsive, communicative, and committed to working closely with clients to achieve their goals.
Final Fantasy
Injection molding manufacturers play a vital role in the production of plastic parts and products across a wide range of industries. By offering expertise in mold design, material selection, process optimization, and quality control, these manufacturers help companies bring high-quality products to market efficiently and cost-effectively. Choosing the right injection molding manufacturer is essential for ensuring the success of any production project, making it a decision that requires careful consideration and due diligence.